切削加工过程的在线监测与自适应控制
- 发布时间:2013/8/23 9:12:04
- 浏览次数:3778
在实际加工过程中,采用传统加工技术选用的加工参数一般过于保守,且无法根据产品实际的加工状态进行加工过程的优化。随着*监控技术与测试手段的不断发展,借助*传感技术、数据处理技术与控制技术等进行复杂数控加工全过程几何信息、物理信息获取、处理,进而发展出加工状态自动判定与优化的智能技术。这类技术一方面集成了车间长期的工程经验,另一方面集成了通过科学分析得到的理论模型,通过两者的结合对实时加工状态进行判断,根据实时工况进行工艺参数的自适应优化,实现连续、稳定、自动的控制加工过程并使其保持*状态,进而获得更高的加工精度和生产效率,从而实现加工过程控制从依赖技艺向依靠科学的方向发展。
关键技术
面向切削加工过程的自适应控制技术需要采用在线或在位的方式对加工过程中的切削力、主轴扭矩、工艺系统振动及刀具磨损等进行实时监测、动态分析、工艺参数优化以及反馈控制。因此,自适应控制技术的实现需要多种技术的支持,包括传感器技术、信号处理技术、基于多传感器信息融合技术、控制决策技术、数据库技术等,其关系如图1所示。

1传感器技术
为了使系统能够在复杂环境中、在无人干预的条件下正常工作,就必须使系统具有类似于人类的信息处理能力,即智能决策。而智能决策需要通过实时监测加工过程来获得信息。在线监测直接面向加工过程,与具体设备和仪器相。因此,适用于加工过程的具有高实时性、高精度和高可靠性的传感器是在线监测的关键。用于加工过程监测的传感器主要有:功率传感器、力传感器、扭矩传感器、声发射传感器、振动传感器、摄像头和激光。
(1)功率传感器。
加工过程中的机床主轴或者驱动电机的功率可以通过功率传感器获得,根据监测到的功率数据,可对功率变化中出现的起伏、波纹、尖峰及短时下降进行判断和预测,从而通过相关算法对功率曲线做平滑处理。此外,主轴有效功率可以表征刀具的切削力,根据切削力与主轴功率的关系,可将实时监测到的主轴功率转换为刀具的切削力,从而获得切削力的实时数据。
(2)力传感器。
为实现对切削加工过程的可靠监视,需要对金属切屑分离过程所产生的力进行地测量和分析,从而识别出切削过程中出现的缺陷,如刀具磨损或断裂,以及加工工件的损伤。切削力的测量可以采用直接法或间接法测量。在直接测量方法中,传感器安装在力的通道中,测量全部力,测量非常准确,与力的作用点无关;在间接测量方法中,部分力通过旁路传递,由于只有部分力作用在传感器上,间接测力系统安装后需要标定,系统的灵敏度与力的作用点有关。
(3)扭矩传感器。
相对于有效功率,主轴扭矩能够更准确地表征刀具的切削力。直接测量机床主轴的扭矩可以获得更的切削力。钻孔、攻丝和多主轴加工过程的监测使用测量主轴扭矩的方法来获得切削力尤为有效。在多主轴加工过程中,每一个主轴上的切削过程所消耗的功率都比总的功率小得多,因此,在这种情况下就不能用有效功率来表征切削力,而是通过主轴扭矩来表征切削力。
(4)声发射传感器。
在切削过程中当刀具断裂时,会产生声发射信号。声发射传感器能监测到在切削过程中产生的声发射信号,通过分析监测到的信号可以获得刀具的信息。声发射传感器对监测小钻头和丝锥的破损尤为有效。在加工过程中传感器可以监测到非常小的声发射信号,再与有效功率或者主轴扭矩相结合,能够可靠地监测到刀具的破损。尤其是在大型机床中监测非常小的刀具以及多主轴加工过程中,更能突显出声发射传感器的优势。
(5)振动传感器。
在切削过程中掉刀、刀具破坏、机械碰撞等会产生异常的振动。振动传感器可以监测切削过程中机床结构产生的振动,通过分析振动可以监测到掉刀、刀具破坏、工件超差、机械碰撞和严重的过程故障。振动传感器也可以监测机床主轴的振动,为加工过程中的振动预测与控制提供数据。
(6)摄像头。
在多主轴加工过程中,分别监测每个主轴成本比较高。这种情况下,可以采用摄像头监测全部主轴。摄像头可以监测20个或更多不同的主轴。在多钻头加工中摄像头可以监测每一个钻头的掉刀和破损。监测系统在学习的时候,记录并存储多钻头的图像,在监测过程中通过比较轮廓来监测每一个钻头。当光学识别系统性能优于基于其他传感器的系统时,它可以用于更多的过程监测,例如检查工装,位置,完整性等。
(7)激光。
当切削刀具过于细小时,出现异常情况引起的波动比较小,使用功率传感器、力传感器无法监测,或者没有合适的位置安装声发射传感器时,可以使用激光光栅。激光光栅可以提供一套可靠的刀具掉刀和破损监测方案。激光光栅也可以监测机床热变形,例如监测加工中心主轴的长度变形。激光的另一个应用是,通过分析工件的反射光监测工件的粗糙度、颤振、切削的波纹等。
2信号处理
传感器在加工现场采集到的模拟信号是不能被监测系统直接使用的,需要转化为数字信号进而转换为有实际意义的物理量。转换过程一般包括转换、放大、滤波、平滑等,这个转换过程需要信号处理的。一般力、声发射和振动传感器都是压电型传感器,需要前置放大器把传感器的电荷信号转换成成正比例的电压信号。声发射放大器从传感器获得原始信号,并提供信号的学习条件、分析方法来增强声发射监测。通过使用放大、过滤和均方根平均,将原始声发射信号转换成有价值的声发射信号,可以在较低的频率下可视化和监测。此外,振动放大器可配备过滤器和均方根转换器,可以过滤掉无意义的噪声获得振动信息。监测系统常用的解决方案是使用单独的为特定类型传感器设计的信号调理放大器。信号调理器封装在一个密闭的盒子里,连接电缆用编织钢网屏蔽保护,这样可以保证他们的抗振动和电气隔离的特性。因此,传感器、连接电缆和调理器可以在恶劣的加工环境下工作。
3基于多传感器的信息融合
由于加工过程中切削条件和切削状态的多样性,导致对切削过程进行准确监控非常困难。传统的基于单一传感器的测量和分析往往难以保证识别精度。为了能够更准确地获得加工过程的状态信息,需要使用多个相同或不同的传感器从不同的方面进行测量。利用不同传感器测量和输出信息的互补性,采用多传感器集成和信息融合技术,将描述同一个加工系统的多个物理量整合成系统的状态向量,为系统的分析与诊断提供更全面的信息,使监测结果更加真实、可靠。
zui简洁的多传感器信息融合方法是,将每个传感器的测量数据单独输入到融合系统中,如果每个传感器所提供的信息反映的是环境中*不同的方面,那么可以将每个传感器提供的信息直接转换为加工系统状态向量的不同分量。该方法的主要优点是融合算法简单,运算量小。如果传感器所提供的环境信息出现重叠,以及可能出现信息的冗余、矛盾和相关,甚至出现其中的某个传感器影响其他传感器的工作,则来自不同传感器的信息就必须在多种表达层次上进行融合,zui终获得加工系统的状态向量。在这种情况下,多传感器信息融合能获得更的状态信息。多传感器信息融合主要有以下几个方面的优点:提高了信息的可信度、增加了系统状态向量的维数、提高了系统的容错能力。
4控制决策
控制系统获得了加工系统的状态信息之后,综合分析加工过程中监测到的数据,获取加工过程中的振动、切削力、切削温度、刀具磨损、加工变形等数据,与理想的加工状态对比。将实际状态和理想状态信息交给内部专家系统处理,专家系统的推理机读取知识库中的经验数据和加工系统自身的信息,分析加工系统的状态信息来判断加工系统的运行状态是否理想。根据加工系统运行状态及切削参数与加工过程振动、变形等因素之间的关系选取优化规则,动态优化工艺参数使加工系统达到更优的运行状态。通过控制器硬件与机床NC系统之间的接口实现对机床主轴转速、进给速度等切削参数的优化控制。专家系统的原理如图2所示。
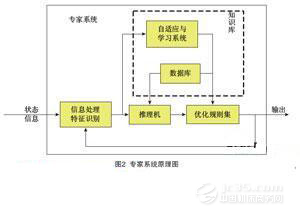
5数据库技术
基于数据库技术的工艺参数库主要包括机床、刀具、工件材料、冷却润滑、加工匹配、零件特征、切削参数、运行状态等信息,其中机床、刀具、工件材料、冷却润滑、加工匹配、零件特征给出了工艺系统的基本信息,切削参数、运行状态描述了工艺系统在不同工艺参数下的运行状态信息。工艺参数库是工程实践中长期积累的经验数据,具有实际应用价值,可以为专家系统的决策提供工程经验。
专家系统将机床、刀具、工件材料、冷却润滑、加工匹配、零件特征等工艺系统信息与切削参数、运行状态的匹配关系作为参数优化的规则,以工艺系统当前的运行状态为基本事实,依据加工过程理论模型及工艺参数库中的经验数据进行演绎推理,zui终得到系统当前的优化参数。专家系统推理机的数据库系统如图3所示。
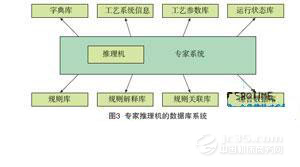
已有产品及应用现状
近年来,国内外针对加工过程的监测与自适应控制技术在航空发动机制造中的应用开展了不同层次的研究工作,典型的商用系统包括OMATIVE自适应控制系统、ARTIS刀具和处理监控系统、BRANKAMP-CNC集成刀具监控、MONTRONIX监控系统、NORDMANN刀具监测与过程控制系统等,这类监控系统所使用的主要传感器如表1所示。

1OMATIVE自适应控制系统
OMATIVE自适应系统将自适应控制技术应用在数控机床上,在加工过程中根据切削力实时优化切削的进给速度,在保证刀具不受损坏的前提下提高加工效率。OMATIVE自适应系统主要功能:提高加工效率;保护刀具、机床、工件不受损害;实时监控、记录切削加工状况。刀具进给速度与切削厚度的关系如图4所示。以色列OMATIVE公司做了大量工件切削对比实验,OMATIVE自适应系统能够大幅提高加工效率。OMATIVE自适应控制系统因其实用性*,现已被国外许多公司使用,如Siemens、Boeing和GeneralElectric等。国内航空航天、纺织、家电等行业的企业也陆续使用该产品。

2ARTIS刀具和处理监控系统
ARTIS刀具监控及机床状况监控系统是由德国ARTIS公司研发的实时在线监控系统。在加工过程中,可准确地检测到断刀、钝刀及掉刀状况。一旦出现异常状况,机床便立刻停机,避免刀具、工件及机床的再一次损伤。采用ARTIS的各种传感器,可对加工及机床状况进行监控。采用不同的监控方式还可有针对性地为用户带来更多益处,如采用ARTIS的自适应控制,不但可对刀具及机床状况进行监控,同时还可以对加工周期进行优化,有效提高机床的加工效率。
3BRANKAMP-CNC集成刀具监控
BRANKAMP监控系统依据特定的监测限度保护设备,任何不规则力的形态都会马上被监测出来,甚至是任何zui微小的误差,在造成主要的伤害之前,这个监测系统立即发现并做出反应,如图5所示。BRANKAMP监控系统为所有的金属切割、冲压、冷锻等制造过程提供过程监测。BRANKAMP主要服务对象包括冲压、冷成型加工、金属切割等加工设备,主要应用于汽车制造行业、紧件加工行业、手机制造业、半导体加工行业、食品和饮料金属包装等行业领域。安装BRANKAMP监测系统可以保护机械设备和昂贵模具,减少废品和设备维修时间,节约成本,提高产品质量,同时具有在线监控以及可视化结果功能。

4MONTRONIX刀具和过程监控系统
MONTRONIX刀具和过程监控系统使用一个或多个压力、扭矩、振动、功率传感器和一个处理器,获得实时的关于切削刀具、机床和加工过程的监控数据。该监控系统可以给制造系统的机床、刀具、工装夹具、加工工件等提供保护,严格控制工件的加工质量,提高加工过程的安全和可靠性,减少加工成本。配套的可视化软件(M-View)使得机器操作者能够快速而地评估加工过程。其图形化显示包括:过程偏差,刀具损坏,逐渐增加的磨损量等,系统可以对这些信息进行记录和评估。该系统可以在加工过程中的任何时候进行可视化显示。
5NORDMANN刀具监测与过程控制系统
NORDMANN的解决方案可对加工过程中的刀具破损、磨损进行检测,对碰撞干涉、刀具负载平衡状态进行监控,从而对刀具和机床进行保护。此外,该系统还可以对工件的非正确装卡状态、错误的工件毛坯尺寸等进行检测并在机床内对工件zui终形状进行尺寸控制,从而保证产品的加工质量。在加工效率方面,NORDMANN监控系统可以通过间接方式对金属切削过程中的有效功率、切削力等进行控制,从而可以减少空切时间、延长刀具使用寿命、zui大化进给与转速以提高加工效率。NORDMANN监测系统可扩展下列额外的测量系统:力传感器、声发射传感器、有功功率测量器、工件的有声尺寸监测、光学激光传感器、直接安装于刀具切入部分的传感器(图6)。在监控过程中,该系统可以实时生成测量数据并显示在PCU50/PCU70模块的操作面板上,并可对刀具的磨损、破损等状态进行评估。应用范围上,NORDMANN监控系统可用于CNC车床、加工中心、磨床等设备加工过程中的功率、力、扭矩等物理量的监测与控制。

结束语
切削加工过程的在线监测与控制系统已在国外广泛应用,并取得了显著的效果。但是,这类系统在国内并未得到广泛应用。随着复杂结构产品的广泛应用、产品服役性能对产品加工质量要求的不断提升,以及生产企业对产品低成本率加工的不断追求,采用相应的监控与优化系统对切削加工过程进行在线监控并进行切削参数的在线优化已逐渐成为智能加工技术研究与工程应用的重点,并将随着数控加工技术以及复杂产品加工需求的发展而得到广泛应用。
(文章来源:航空制造网)