以高品质高性能和专业的技术赢得市场
- 2022-08-18 14:01:445618
来自德马吉森精机集团的各类机床,尤其在加工刚性和加工能力上非常适合航空航天行业的各种复杂结构和高精度的零件加工。

航空航天行业的零部件结构复杂、材料切削难度高,精度要求高,对机床的定位精度、主轴刚性、柔性加工能力等都提出了较高要求。针对这些要求,德马吉森精机集团在世界范围内率先开发了带车削功能的五轴铣车加工中心。它的回转工作台采用了伺服电机直接驱动技术,最高转速可达1,200rpm。
该技术在2006年成功运用在沃尔沃宇航瑞典工厂,成为世界第一条五轴铣车加工中心柔性线。该柔性线通过立车和五轴铣床功能的完美结合,使得客户在加工航空发动机机匣和盘环类回转体零件时,零件不需要在车床和铣床等不同类型的机床上转换,从而减少了重复定位误差,并省略了零件二次装夹找正和零件的周转等待时间。使得客户的工艺流程大大缩短,从而大大提高了零件的生产效率,并且进一步保证了加工精度。同时客户现场的机床种类及数量也同步减少,大大改善了生产车间的现场管理。
迄今为止,德马吉森精机对于该铣车技术已有超过20年的生产制造经验,全球累计销量超过1,800台,其中近500台广泛服务于中国航发,美国GE航空,法国赛峰,英国罗罗及普惠发动机等世界最优秀航空发动机制造企业,并且深得信任及好评。
众所周知,为了减轻飞行器自身重量,航空航天行业有大量的铝合金材料零件。其中各类壁板及肋板零件在加工过程中的金属去除率会高达95%以上。对此传统的高速电主轴已经不能满足客户需要的高效加工能力。对此中国航空工业,美国波音公司及欧洲空客公司等顶级飞机制造企业选用了德马吉森精机集团专门针对航空航天行业开发并自己生产的主轴输出功率高达100kW,最高转速为15,000rpm配备HSK-A100刀柄的电主轴。该自产主轴在满功率输出时,可以帮助客户最大程度的提高铝合金零件加工效率,降低了制造成本。
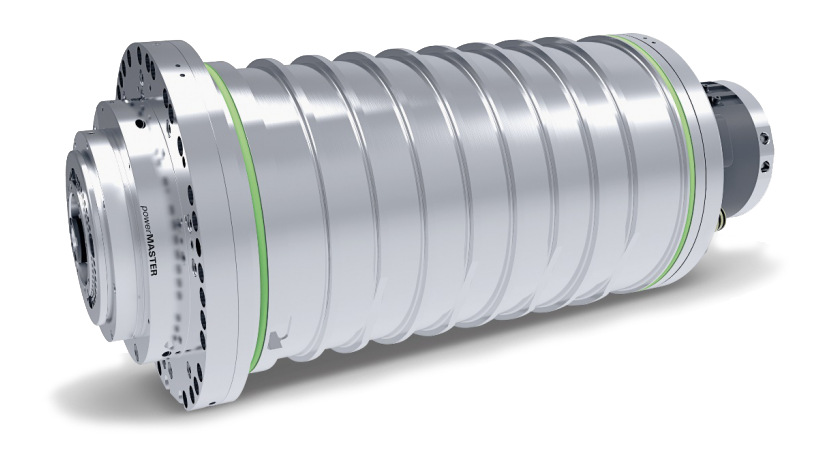
针对钛合金及不锈钢等材料的飞机零件加工,我公司开发了可以实现B轴联动的大扭矩机械主轴,最高转速为8,000rpm,最高扭矩可达1,800Nm,该自产主轴适用于我公司多款五轴联动加工中心,非常好的满足了复杂结构零件高效率粗加工及高转速精加工的全部要求,因此也得到了国际知名的起落架制造商德国利勃海尔公司,法国赛峰集团等用户的青睐。
为了满足航空航天制造行业对于数字化产品的需求,德马吉森精机集团基于德国工业4.0技术标准的要求,针对不同的应用领域,已经开发出了62个面向市场的技术循环产品。包括应用于机床自身精度矫正功能,如3D quickset(机床快速三维校正功能)可以在数分钟内完成机床精度的快速校准,以保证机床快速恢复精度状态,确保零件的加工精度。
又如在工件精度检测方面,开发了应用于发动机机匣特殊部位,采用特殊测头的测量循环,以保证机床在线测量功能的便捷性与实用性。再如针对快捷编程方面,专门开发了更易于5轴联动加工编程的技术循环,使得用户编程人员节省大量的重复性工作,大大的提高了工作效率。基于这些优势,众多功能已经广泛应用于航空航天行业的制造企业。

德马吉森精机集团不仅注重客户对于机床硬件和数字化产品的需求,同时为了满足航空航天行业客户在材料、结构、工艺方面的特殊技术需求,专门成立了“航空航天卓越技术中心”。
该中心实现了以下几个方面的作用:第一,解决客户现有的技术问题、满足其加工要求而进行的一系列技术方案的设计和交钥匙工程。第二,根据航空航天行业的发展趋势进行一些预研工作。比如针对一些新材料的应用,中心会对这些材料在各种参数方案下(包括机床参数、刀具参数、切削工艺参数等)进行试加工,得到最优化的工艺参数,以便为客户提供更有针对性的解决方案。第三,中心定期安排经验丰富的应用工程师与用户进行现场交流,提供技术支持,确保客户可以充分发挥机床的潜在性能。第四,作为试验机构,针对航空航天行业特殊的材料、结构和工艺进行加工试验,并将得到的数据反馈给机床的设计部门,帮助设计部门改进机床设计,进一步提高新一代机床对于航空航天零件加工的适应性。
德马吉森精机集团不仅仅是机床的供应商,更是航空航天行业加工制造方案的提供者。同时也通过与最终用户的良好沟通和服务,使得我们与最终用户共同成长,并得以成为最终用户最忠实的合作伙伴。