德国汉特曼集团联手布勒,正式进军一体化压铸
- 2022-06-09 10:43:355048
【机床商务网栏目 名企在线】近日,德国轻金属组件解决方案供应商汉特曼(Handtmann)宣布将引入一体化压铸技术,并投资购买了布勒Carat 610压铸岛。
汉特曼宣称,Carat 610压铸岛61,000kN的锁定力和高达128kg的铝注射重量,使其非常适合于大型结构件的生产,例如电动汽车的大型电池外壳或整个后或前底板。
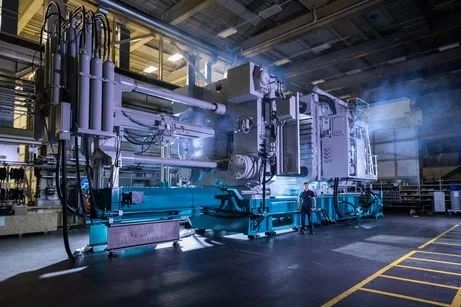
01、一体化压铸技术的魅力
在过去十几年,汽车制造界习惯使用冲压为汽车生产车身零部件。汽车车身是指车身覆盖件焊接或铆接在车身骨架上形成的完整壳体,由车身焊接总成(白车身)及其附件组成,一个完整的白车身主要由前围总成、侧围总成、地板总成,顶盖总成、后围总成及四门两盖组成。传统汽车制造工艺分为4个环节:一是冲压,利用不同的压机,完成车门、左右侧围、机舱盖、前后底板、顶盖、后背门及各种冲压小件的制造;二是焊装,将冲压完成的车身围件焊接在一起,完成白车身的制造;三是涂装,对白车身进行各种防腐处理,并喷涂上漂亮的色漆、清漆,以达到上色和表面防护的作用;四是总装,将车身上各种零部件及系统安装在车身上组装成一台完整的汽车并进行点检、路试等一系列测试,最终下线成为合格商品车。
一体化压铸技术就是以单个大型铝铸件替代原本十几个或者几十个小型零件,相当于覆盖了冲压和焊接两个步骤。其基本工作原理是将熔化的铝液灌入高压模具,待铝液冷却后凝固,再将其放入水中加速冷却,随后利用高功率激光器进行后续处理与质检,这样成型的铸件就能用于汽车的制造。
关于一体化压铸的优势,马斯克曾经用“更轻、更紧凑、更低的投资、更低的单位成本”来形容。

首先,压铸机的占地面积小,这使得基础设施成本大幅降低。压铸机一次压铸加工的时间仅为80~90秒,每小时能完成40~45个铸件,一天能生产1000个铸件,而传统工艺冲压焊接成一个部件至少需要两个小时。由于应用了新的合金材料,压铸件的表面粗糙度可达Ra0.8-3.2μm,足够光滑,基本不用再进行机加工。一体化压铸技术显著减少了生产的时间成本后,基于产流程的简化,所需的技术工人至少能缩减到原来的十分之一。
第二,以整体性部件代替冲压和焊接的多个车身围件,可以有效避免大量零件焊接时的误差累计。压铸零件将车身匹配的尺寸链缩短至两到三环,尺寸链环越少,车身精度的影响因素越少,车身精度的实现和稳定性也越好。加之数控加工技术,整车精度提升至微米级别。
第三,一体化压铸技术只使用一种材料,全铝车身的材料回收利用率可以达到95%以上。一体化压铸零部件由金属液一次充型完成,材料单一。回收时可直接将废料融化制造其他产品,保证了白车身制造过程中极高的原材料回收利用率。而运用传统制造工艺,在制造白车身时混合使用多种材料,每一个零件的种类(钢、铝)、牌号、金属元素的含量都不一样,报废后的整车白车身只能作为炼钢炼铝的原材料,无法直接整体回炉后制造新的产品。
第四,一体化压铸能使车辆轻量化,因为一体化压铸用的铝合金材料是轻量化的最佳解决材料。当铝合金用量达到250公斤时,就相当于减少了500公斤的汽车用钢量。根据国际铝业协会的计算,纯电动车用铝最高可达361.3公斤,占整备质量的33.1%。以一辆1.5吨的乘用车为例,就相当于在现有水平上减少了30%左右的重量,可将燃油效率提高20%以上。实验证明,如果减重10%和15%,汽油乘用车可分别减少油耗3.3%和5%,柴油乘用车的油耗分别减少3.9%和5.9%,电动车(包括插电式混合动力车)则能分别减少电能消耗6.3%和9.5%,其中轻量化对电动车的促进作用最为明显。在电池技术暂时难以有质的突破前提下,新能源电动车车身轻量化无疑是进一步增加续航和解决里程焦虑的最佳选择。
碳减排是目前汽车行业面临的最大难题,影响了车企们在新能源车型的偏重以及在原材料和工艺上的选择。传统的钢铝合金和钢制底盘需要通过多家多级采购部件,一体压铸车身选择碳足迹很低的铝材(每公斤低于4公斤的二氧化碳的排放量),碳排放更低也更可控。除了减少生产过程中的碳足迹,更重要的是一体化铸造技术还有助于减少汽车离开装配厂后对环境的影响。用这种新技术生产的电动汽车重量更轻,驾驶时消耗更少的电力,减少轮胎、刹车和路面磨损等非尾气排放。
02、长期合作伙伴关系
Carat 610压铸岛将补充到汉特曼在德国南部比伯拉赫(Biberach a. d. Riss)的工厂中。这标志着这家欧洲一级供应商首次进军一体化压铸领域。“我们很自豪能成为欧洲这一里程碑的一部分。它清楚地表明了一体化铸造对整个压铸行业的重要性,”布勒压铸总经理Cornel Mendler说,“通过将应用范围扩展到车身部分,一体化铸造再次推动了结构铸件的发展。”
Carat 610并不是汉特曼对Carat系列的第一笔投资。汉特曼在德国、斯洛伐克和中国的工厂中有近70台布勒压铸机在运行,其中50台是Carat两模板系列压铸机。汉特曼于2007年首次购买该型号压铸机,当时该系列刚刚推出。与前代产品相比,其紧凑的设计及易用性使其备受欢迎。Carat系列在为汉特曼生产汽车结构件、电池和变速箱外壳等铸件时的结果也令人满意。
据悉,汉特曼比伯拉赫工厂的改造和Carat 610压铸岛的调试计划于2023年完成。