HTM系列卧式车铣复合加工中心的研发与应用
- 2020-06-17 13:49:529778
【机床商务网栏目 科技动态】HTM系列卧式车铣复合加工中心的研发与应用。
一、产品概述
卧式车铣复合加工中心作为机床行业的高档机床之一其市场需求巨大,在提高能源、航空、航天、船舶及军工等行业一些关键零件的加工精度和加工效率方面具有不可替代的作用。
沈阳机床HTM系列卧式车铣复合加工中心是针对汽车、航天、军工等行业高档数控机床的需求而研制开发的,该机床以“零件单机完工”为设计宗旨,融合了车削中心与卧式加工中心的优点,采用X1、Y、Z1三个直线轴正交结构,加大的Y轴行程很好地扩展了机床的加工空间。与可以连续分度的车削主轴(C轴)和在240°范围内摆动的铣削主轴(B轴)配合,能进行五轴联动加工,极大地改善了机床对复杂零件的加工能力。
机床配置自动换刀机构,车、铣主轴采用大功率电主轴驱动,工件一次装卡调整后,不仅能进行车削、铣削、钻削、磨削等多工序的复合加工,利用多轴联动功能还可完成零件倾斜部位及复杂空间曲面的加工,极大地提高了加工效率与精度。
HTM系列卧式车铣复合加工中心体现了当今数控机床高效、高精、复合化的发展趋势,尺寸公差为IT6级;加工表面粗糙度Ra1.6μm,圆度为3.5μm,该机床的显著特点是铣削加工叶片螺旋面、加工偏心零件、铣削斜面等,特别适用于复杂零件的加工。
二、新技术的应用情况
现代数控机床的主要特征为高速、高精度和高动态特性,沈阳机床对HTM系列车铣复合加工中心动态性能展开研究,通过借鉴国内外机床动态特性测试手段以及机床整机仿真分析等方法,为高档数控机床的性能评估及改善,为结构优化提供依据;基于现有机床原型构建机床动力学模型分析计算,并针对机床主要部件进行结构优化改善整体动态性能。
沈阳机床紧紧围绕重点用户领域需求,进行高速车铣复合、铣削主轴、高刚性高定位精度B轴技术及热变形误差补偿技术的研究开发,攻克了一系列技术难题。
1. 高刚性高定位精度B轴技术
通过对高刚性高定位精度B轴技术的研究,解决了三个关键技术问题,即B轴高定位精度的实现方式;B轴高刚性的实现方式;小空间内B轴附属功能的实现方式。B轴的驱动依靠安装在主轴上的大转矩、高可靠性的力矩电机来完成,外环配有水套,实现力矩电机的循环冷却,控制B轴温升。
主轴旋转分度时,依靠转台轴承进行回转支撑。主轴后端配有高精度直联反馈光栅,保证B轴的分度精度。该B轴装置有两种锁紧固定方式,当B轴分度角度是2.5º的整数倍时,通过轴承前端的锁紧齿盘进行固定;当B轴分度角度不是2.5º的整数倍时,通过B轴后端的刹车机构进行锁紧。在B轴参与插补加工的过程中,如果出现振动,可以对B轴后端的刹车机构进行低压控制,使其起到增加减振阻尼的作用。B轴装置后端有复杂的液压、冷却、气动配给装置,保证B轴装置及车削主轴功能的实现(见图1)。

图1 B轴机械图
为提高B轴控制精度和响应速度,对原有产品进行升级改造,更改B轴结构,HTM63系列车铣加工中心采用力矩电机式B轴(见图2)代替机械式B轴结构形式(见图3)。相比机械式B轴具有以下优点,传动链减少,以力矩电机结构代替原齿轮传动结构,减少了减速变速、齿轮传动、齿轮定位等环节和零件;在保持B轴扭矩不变的情况下,提高系统传动效率及响应速度,便于加工制造和压缩装配调整时间,提高装配效率,减少装配误差;提高B轴动态响应能力,减少响应时间,提高加工效率,增加使用可靠性和稳定性。

图2 力矩电机B轴结构 图3 机械B轴结构
机床主轴采用高速、高可靠性的内装电机实现直接驱动,反馈光栅直联结构,保证车削主轴的高动态特性;主轴箱体内置水套,对电主轴进行循环冷却;车削主轴前端布置液压锁紧机构,保证了工件任意角度定位进行铣、钻加工时的锁紧刚性。电主轴主轴箱如图4所示。

图4 电主轴主轴箱
对主轴刀具高压内冷进水结构也进行了改进,原结构在使用一段时间后,受机加件加工精度的工作影响,存在漏水问题,影响使用寿命。将原结构改为旋转接头,靠高压水压力自动密封接头,有效解决了结构漏水,提高了使用寿命,增加密封可靠性。
HTM63系列车铣加工中心副主轴锁紧装置改进为滑块锁紧,床身加高更改内部筋型,B轴三齿盘锁紧机构由外布置改为内布置结构。第二主轴锁紧原为液压压板结构,布置在床身内侧。使用中发现问题为当有铁屑或油污进入床身内部后,会造成锁紧失灵,不在正确位置锁紧;后采用锁紧滑块形式,通过对导轨锁紧达到定位锁紧目的。这种锁紧形式安装、调整、维护和使用方便,定位锁紧安全可靠,精度和可靠性高。
针对原床身刚性不好,装配后床身精度不好等情况,重新设计床身内部结构。原床身结构如图5所示,内部为1条筋型支撑,床身整体变形量大;通过计算分析机床受力点和变形量大点,通过软件模拟分析增加床身内部筋型,调高床身高度等设计改进,增强了整体刚性,减小了床身变形量,达到提高机床精度、可靠性的目的,同时提高了床身固有频率达到远离机床共振点,避免切削共振产生。改进后床身结构如图6所示。
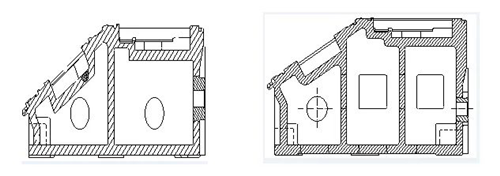
图5 改进前床身结构 图6 改进后床身结构
B轴原分度锁紧机构布置在滑枕外侧,裸露布置。易受到油气污染锈蚀,同时原铣削头,受机构整体变形影响锁紧时锁紧角度误差容易超差,精度保持性不好。本次改进将锁紧机构整合在B轴箱体内部,靠近铣削头处,B轴整体全防护,锁紧机构使用精度和寿命得到提高,同时增强机构运行可靠性和稳定性。HTM80150机床如图7所示,HTM63150iy机床如图8所示。

(a)外部展示图
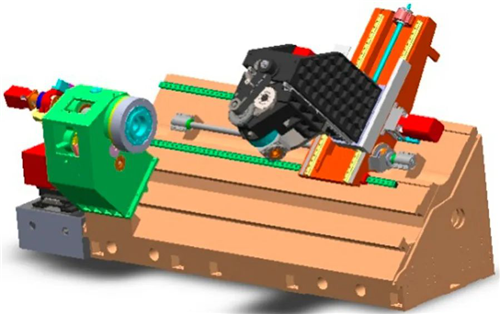
(b)部分结构示意图
图7 HTM80150机床

(a)正视图 (b)机床侧视图
图8 HTM63150iy机床
2.车铣复合加工中心动态性能测试及拓扑优化
通过对车铣复合加工中心动态性能展开研究,借鉴国内外机床动态特性测试手段以及机床整机仿真分析等方法,实现高档数控机床的性能评估及改善,为结构优化提供依据。基于现有机床原型构建机床动力学模型分析计算,并针对机床主要部件进行结构优化改善整体动态性能。
(1)模态测试
综合模态分析方法即用模态试验的结果来验证和校正模态仿真的设置。由于在模态仿真中需要设置模型的材料参数、边界条件和结合面部件等效参数(包括滚珠丝杠、滑块导轨、轴承),变量较多,各变量对于仿真结果的影响机理较为复杂。鉴于此原因,我们在进行模态试验时采用边装配边进行模态试验的方法,也即当装配一个部件时即进行模态试验并进行模态仿真,并用模态试验校正仿真参数,这样就确定下该部件的仿真参数。当再装配下一个部件时同样进行模态试验和模态仿真,这样只需要调整下一个需要装配的部件的仿真参数。由此,便于控制模态仿真过程中的单一变量,减少误差。
将各个机床部件参数导入机床整机模型进行仿真,得到机床的整机模态性能如图9所示。
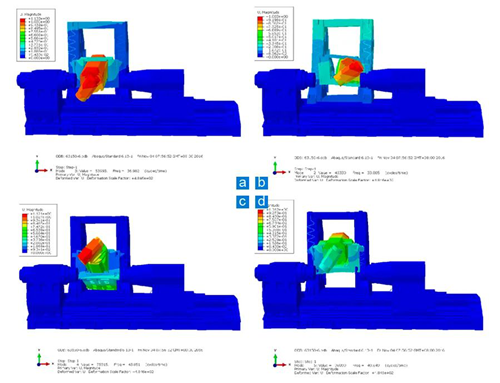
(a)机床整机一阶模态图(b)机床整机二阶模态(c)机床整机三阶模态(d)机床整机四阶模态图9 机床整机各阶模态
从以上整机模态仿真结果可以看出,机床第一阶的振动频率为33Hz,振型为铣主轴结构的振动变形和立柱结构的振动变形,二阶振型也为立柱结构与铣主轴结构的振动变形。需要对机床相关部件进行优化和改进。
(2)立柱轻量化
机床立柱结构的优化目标为:低阶固有频率高、运动部件质量小、兼具体积与效率。
对机床立柱的箱体式结构进行相应的优化和改进,如图10所示。将机床的箱体式结构修改为开放式结构,将箱体式结构的垂直交叉肋板修改为更为稳定的斜交叉肋板,并加一些肋板进行加固。采用该结构材料节省0.03m3,若是采用铸铁材料,重量减轻约210kg。

图10 轻量化立柱结构与剖视图
使用该立柱结构对机床进行模态仿真,该模型设置与机床原仿真模型设置一致,仅将原模型中的立柱结构换为经过改进的机床立柱结构。仿真结果如图11所示。

图11 机床立柱仿真结果(部分略)
(3)铣主轴结构优化
固有频率较低说明结构的结构刚度较小,或者承载质量较大。提高结构的刚度或降低结构的承载质量,都可以提高机床的固有频率。根据研究对象的设计,机床的铣主轴长度仅为350mm,可以节省更多的空间,机床的加工空间更大,同时在不降低输出功率的情况下,该型号主轴的功率密度更高,质量更轻,对于机床的动态特性更有利。
对比机床原设计动态特性仿真分析结果以及铣主轴经过改进设计的机床动态特性结果,见表1。

从表1对比分析可以看出,采用新主轴的设计结果,机床各阶次的频率都有提升,对铣主轴振动的阶次的振型尤其明显,高阶模态频率提升也较明显。
(4) 结构拓扑优化
此次对结构拓扑优化的流程如图12所示。

图12 拓扑优化流程
在HTM3150iy的床鞍结构研究中,进行了结构尺寸优化的研究工作。如图13所示,其中,x1为两侧板厚度,x2为前侧板厚度,x3为底板厚度,x4为背部肋板厚度,x5为底部肋板厚度。其优化变量见表2。

图13 HTM3150iy床鞍结构
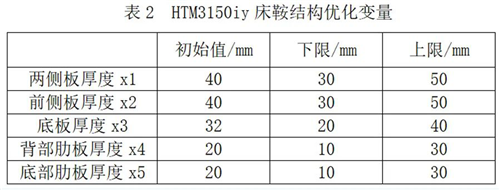
根据设计变量的变化范围,采用拉丁超立方设计方法,使试验设计矩阵中各个样本点因素水平分布尽可能均匀,得到15组试验数据,并对得到的数据点进行仿真,形成床鞍性能评价指标样本(见表3)。
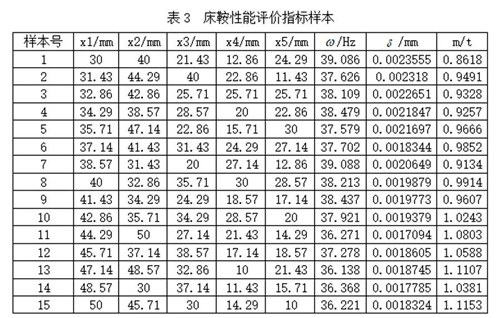
通过表3,借助Isight软件建立RBF近似模型,并根据所建立的RBF近似模型,基于帕累托法则,得到输入输出的帕累托图(见图14)。

(a)设计变量与机床一阶固有频率的帕累托图

(b)设计变量与大变形量的帕累托图

(c)基于RBF近似模型的设计变量与质量m的帕累托图图14 设计变量与响应的帕累托图
利用RBF近似模型进行优化分析,借助优化算法,得到优解,为了方便铸造,对尺寸进行一定的改进。并基于原始有限元模型,将设计尺寸改为优化改进后的尺寸,重新生成模型,并进行静力分析和装配条件下的模态分析,得到的结果如表4所示。

由表4可以看出,经过优化改进后机床一阶固有频率提高了4.24%,大变形量减小了3.83%,同时床鞍的质量减轻了94kg,减少了9.4%。此次优化在减轻了床鞍质量的前提下,同时提高了一阶固有频率,并且降低了机床床鞍大变形量,且结构的静动态特性有所加强,因此该尺寸优化改进是可行的。
采用变密度法,经过有限元分析及迭代计算,得到机床床鞍结构拓扑优化结果,其密度云图如图15、图16所示,红色区域为密度大的材料需要保留,蓝色区域为密度小的材料,对结构性能影响相对较小,可以尝试去除。
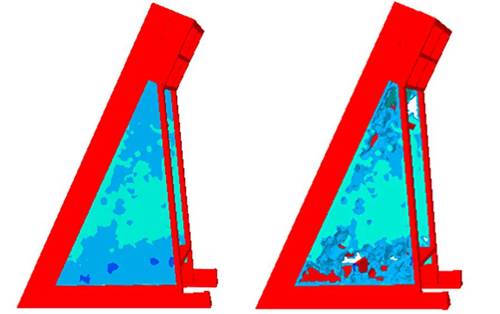
图15 床鞍密度云图 图16 床鞍拓扑优化结构
从铸造工艺及加工成本方面进行考虑,根据床鞍拓扑优化的结果,兼顾铸造方便性及可行性,建议分别在两侧板的下部开两个圆孔,在两侧的上部开一个孔,改进后的结构如图17所示。

图17 拓扑优化改进后结构

通过表5可知,进行拓扑优化后,机床的一阶固有频率有所提升,并且大变形量变化很小,且比原结构的大变形量小,同时床鞍的质量又减少了3.6%,达到了设计目的,因此该设计是合理的。
三、成果应用及推广情况
在研发HTM系列卧式车铣复合加工中心的过程中,开展了机床结构优化技术、热变形误差补偿技术、多轴联动车铣复合加工工艺、可靠性技术、在线检测技术、三维防碰撞技术、动态性能研究与测试技术、空间误差补偿技术、高刚性高定位精度B 轴技术和带刀具自动识别系统的自动换刀技术的研究。对于以上关键技术的研究,对车铣复合数控加工设备的研发和生产提出了重要的参考和指导要求。
车铣复合加工设备的精度及其性能指标直接影响了产品的加工精度。车铣复合加工工艺设计对车铣复合加工设备的性能依赖性更大,车铣复合加工设备的主轴数目、刀架数目、主轴与刀架的相对位置关系都对车铣复合工艺有很大影响。因此,为了完成高精度的产品加工要求,车铣复合数控加工工艺设计及其仿真或实际加工可以有效检验车铣复合加工设备的精度和参数指标。
在车铣复合加工机床研发方面,可考虑解决现有的车铣复合工艺设计问题,如工艺设计过程中,易出现刀架上的非加工刀具与工件或机床干涉的问题,可考虑将刀架改为刀塔,并建立刀具库,不仅提高了加工过程中可携带的刀具数量,而且大大减少了发生干涉碰撞的概率。
在车铣复合加工机床的生产装配方面,车铣复合加工工艺对机床刀架、主轴的位置精度、双主轴之间的位置精度、双刀架之间的位置精度等方面提出了具体的要求,合理安排车铣复合加工设备装配工艺,保证车铣复合机床的精度要求。如HTM63系列车铣加工中心是沈阳机床自行开发设计HTM系列五轴车铣中心的更新换代产品,具有先进水平。该车铣中心除了可以实现直线、斜线、圆弧、锥螺纹及多头螺纹外,还可进行铣直、斜面,铣螺旋槽,铣螺纹,以及镗、铣钻等多种加工方式,特别适合于军工、航空航天、船舶、运输等行业对高精度、形状复杂的大型回转体零件加工的要求。
同时在产品研发与产业化过程中,同相关用户紧密联系,针对卧式车铣复合加工中心的几个典型样件,进行车铣复合工艺研究与示范应用,实现一次装卡中完成回转车削、斜面及曲面铣削、斜孔及孔口倒圆加工等多道工序。
掌握和优化用户加工工艺,努力开拓市场需求空间,始终把用户的需求放在第一位,通过解决终销售问题,保证了产业化目标的实现。