什么是金属螺纹加工?
- 2020-04-13 10:10:2311924
【机床商务网栏目 科技动态】螺纹的主要功能是为了实现机械耦合,通过将旋转/线性运动转化为线性/旋转运动来传递运动,实现机械效益。
螺纹牙型定义了螺纹的几何形状,这其中包括零件直径 (大径、中径和小径)、螺纹牙型角、螺距、半径和螺旋升角。每种螺纹加工方法和刀具在特定情况下都有他们自身的优点。今天我们就来详细探讨一下金属车削加工螺纹的知识和要点。
一、螺纹加工重要基本知识
1. 术语定义

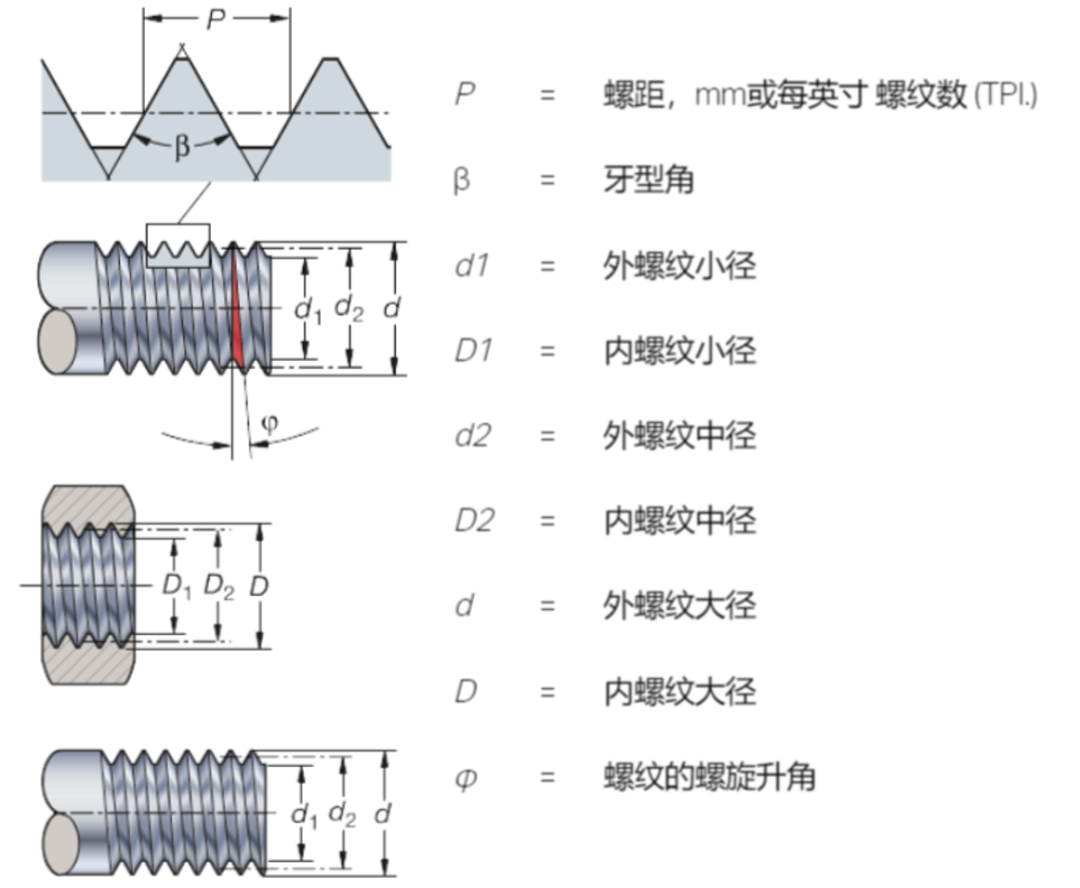
①牙底 ②牙侧 ③牙顶

螺旋升角:
- 螺旋升角取决于螺纹的直径和螺距。
- 通过更换刀垫调整刀片的牙侧后角。
- 刃倾角为γ。常见的刃倾角为1°,对应刀柄中的标准刀垫。
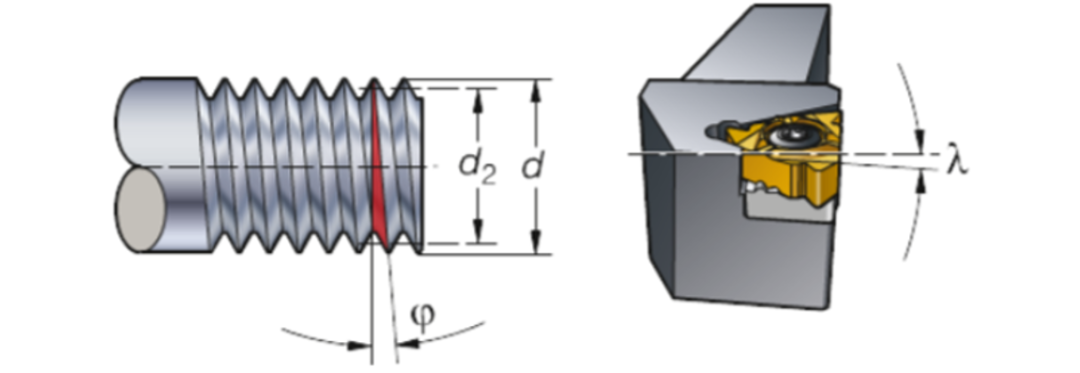
切入和切出螺纹时的切削力:
- 螺纹加工工序中的高轴向切削力在切削刀具切入和切出工件期间出现。
- 切削参数过高可能导致夹紧不可靠的刀片出现运动。

倾斜刀片以获得间隙:
可以在刀柄中的刀片下方利用刀垫设置刃倾角。参考刀具样本中的图表选择使用哪种刀垫。所有刀柄都配备刃倾角设置为1°的标准刀垫。
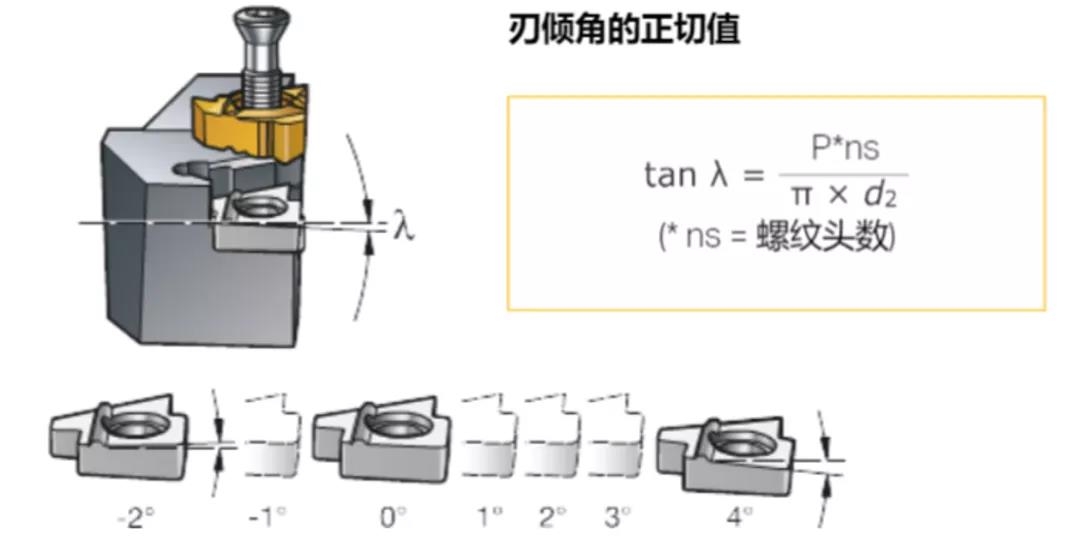
根据刃倾角选择刀垫。工件直径和螺距会影响刃倾角。从下图可以看出,工件直径为40mm,螺距为6mm,所需的刀垫必须具有3°刃倾角(不能使用标准刀垫)。
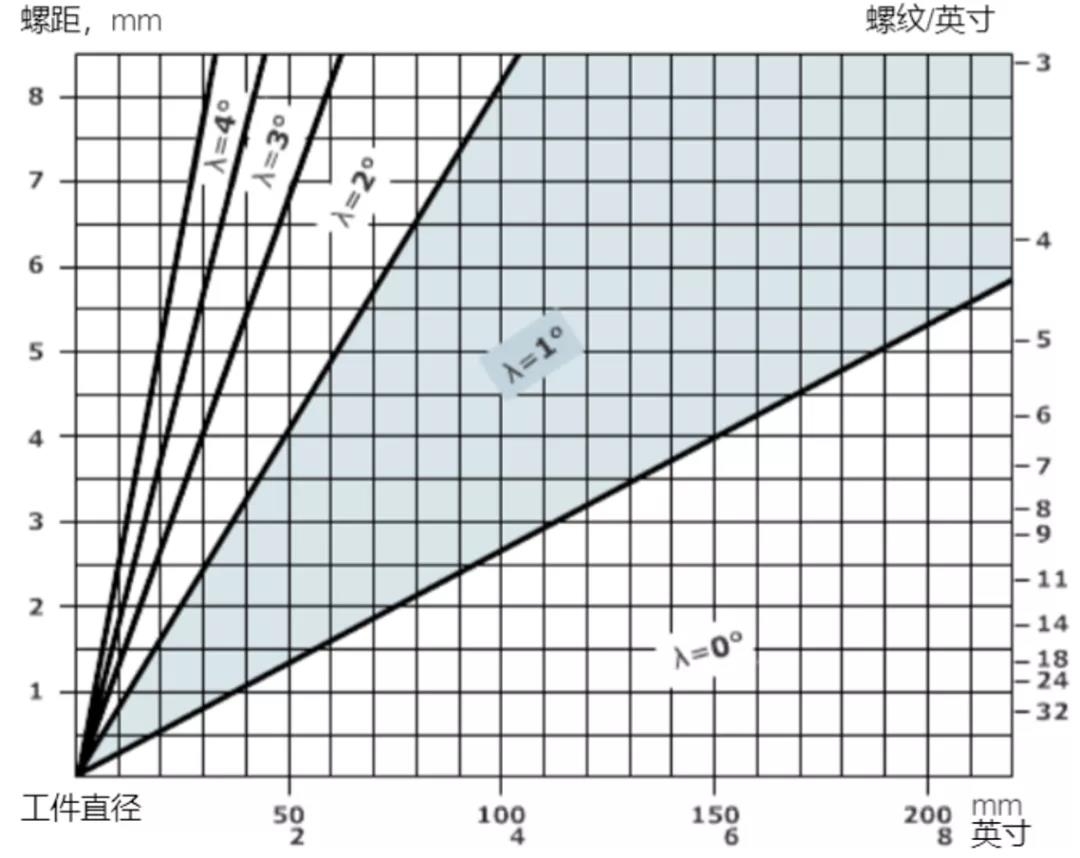
螺纹加工刀片和刀垫的标记:
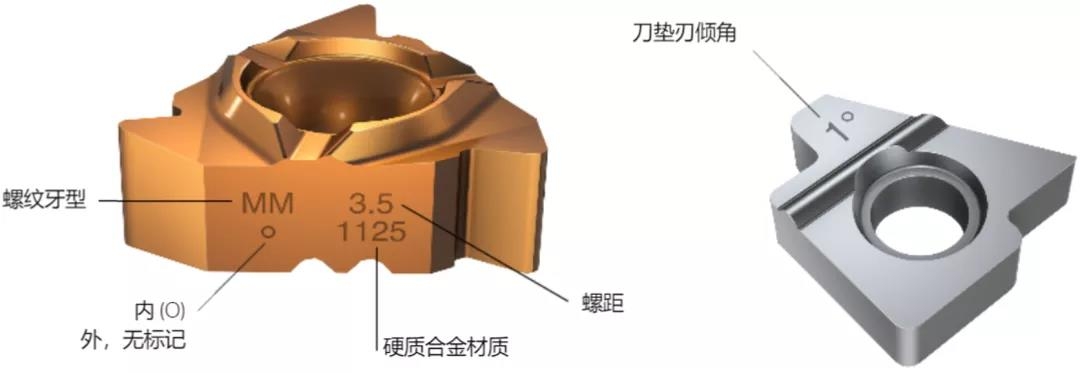
螺纹形状及相关应用:
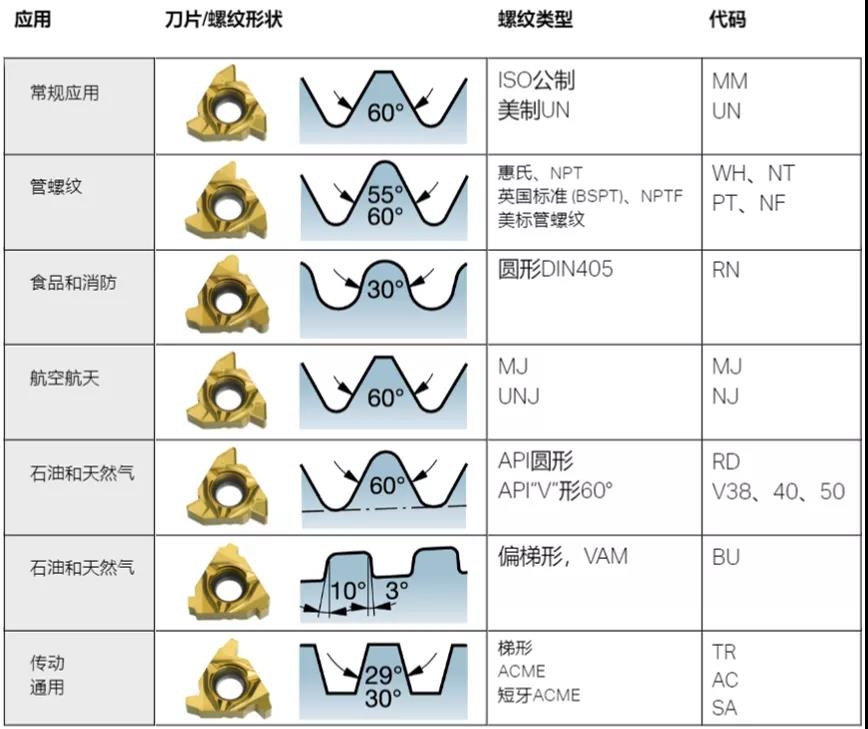
二、螺纹刀片类型及夹持方案
1. 多牙型刀片

优点:
- 减少进刀次数
- 非常高的生产率
缺点:
- 需要稳定装夹
- 在加工完螺纹之后需要足够的退刀空间
2. 全牙型刀片
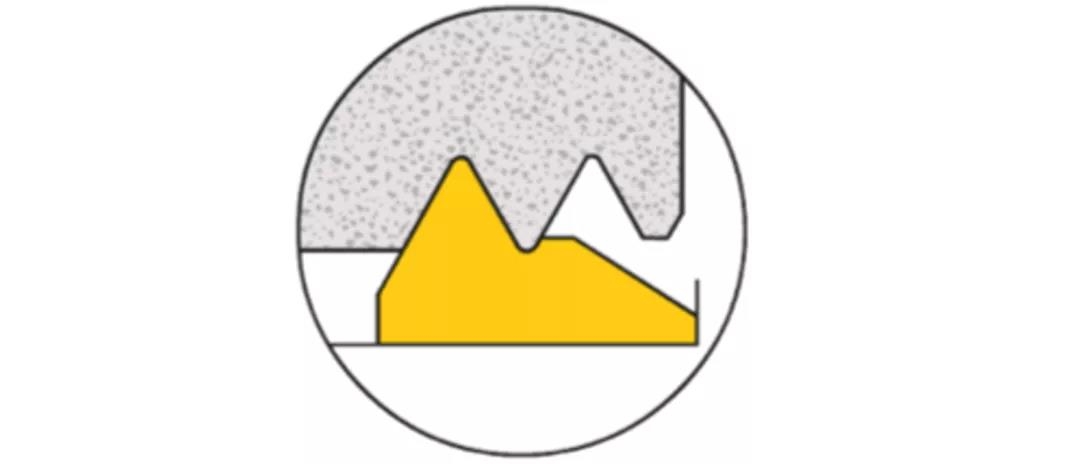
优点:
- 更好地控制螺纹形状
- 毛刺更少
缺点:
- 一种刀片只能切削一种螺距
3. V牙型刀片

优点:
- 灵活性,同一种刀片可用于加工几种螺距。
缺点
- 会导致毛刺形成,需要去除毛刺。
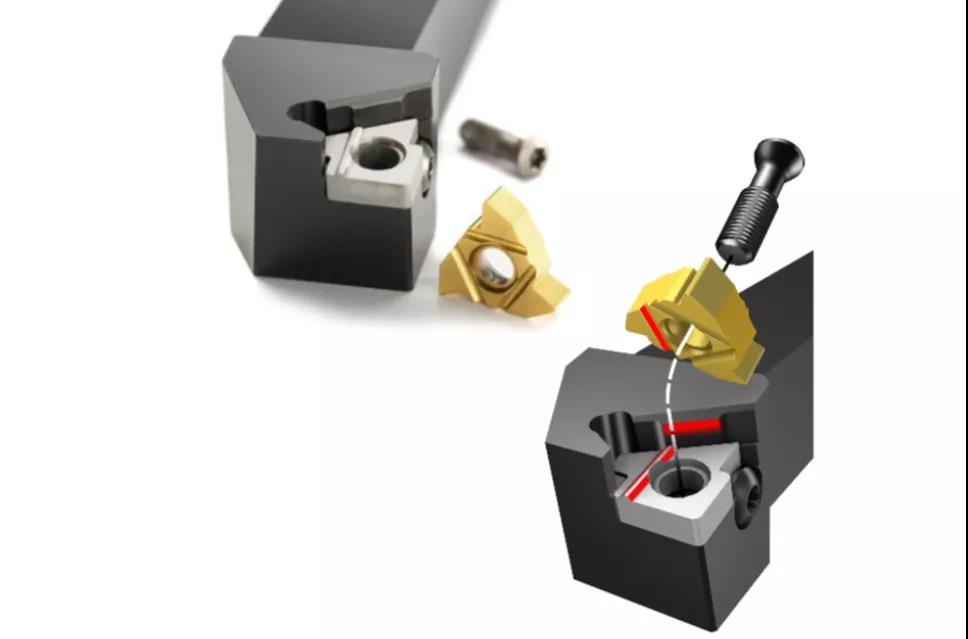
各式各样的刀柄:

三、三种不同类型的进刀方法
进刀方法可对螺纹加工过程产生重大的影响。它会影响:切削控制、刀片磨损、螺纹质量、刀具寿命。
1. 改进式侧向进刀
大多数数控机床都能通过循环程序使用这种进刀方法:
- 切屑与传统车削类型-更易成形和引导
- 轴向切削力可降低振动风险
- 切屑较厚,但仅与刀片的一面相接触
- 传递至刀片的热量减少
- 大多数螺纹加工工序的首选
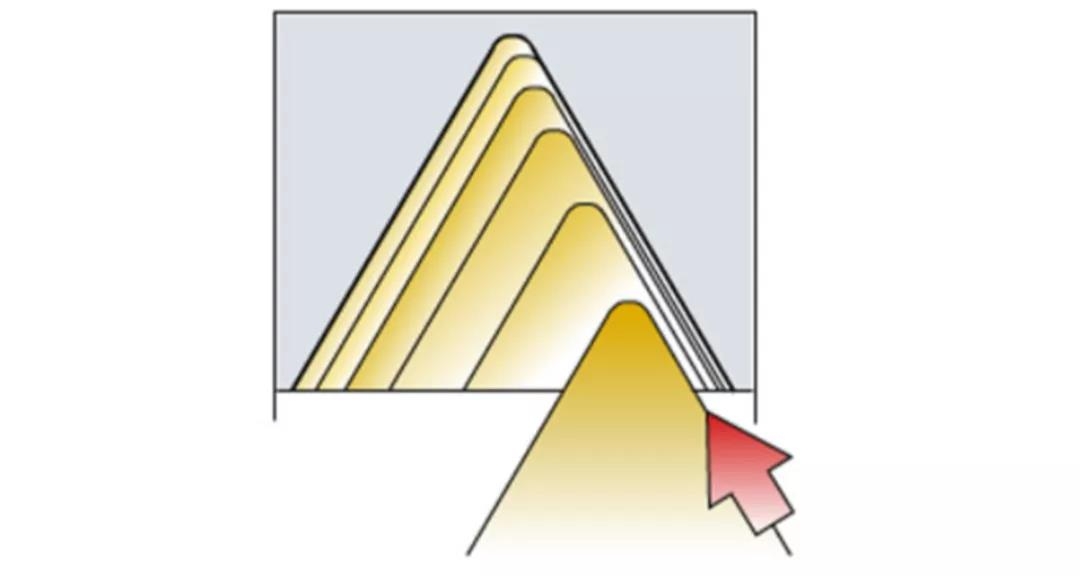
2. 径向进刀
常用的方法-较早的非数控车床能够使用的方法:
- 产生坚硬的“V”形切屑
- 均匀的刀片磨损
- 刀片座暴露于高温下,从而限制了进刀深度
- 适合加工细牙螺纹
- 在加工粗牙螺纹时可能产生振动且切屑控制差
- 加工硬化材料的首选

3. 交替式进刀
- 推荐用于大牙型
- 在加工螺距非常大的螺纹时能够实现均匀的刀片磨损和长刀具寿命
- 切屑被沿着两个方向引导,因此难以控制
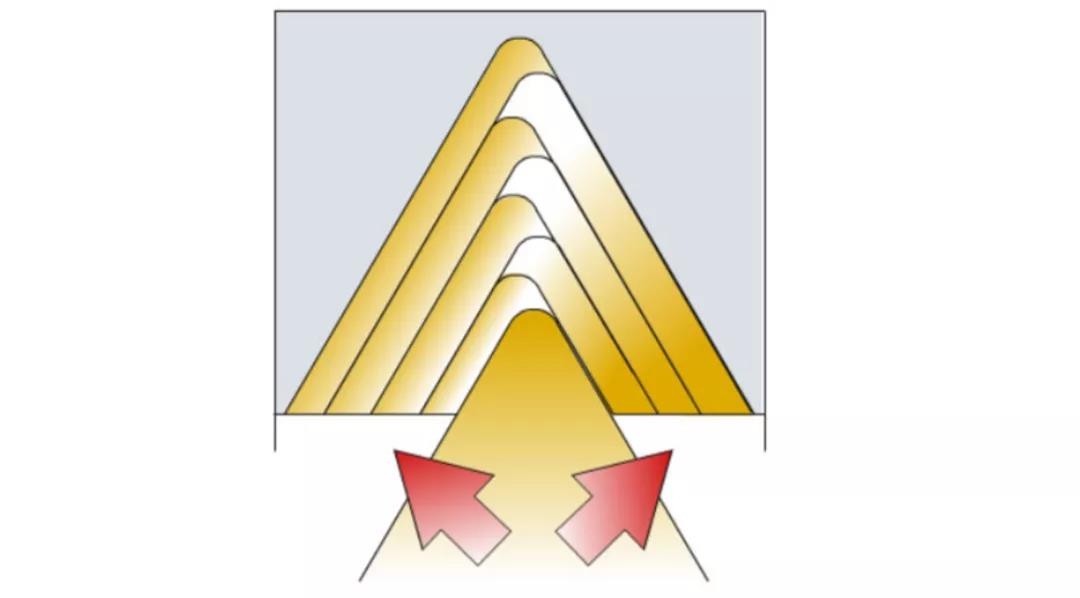
四、改进加工结果的方法

切深逐层递减(左)、切深恒定(右)
1. 切深逐层递减(切屑面积不变)
能够实现恒定的切屑面积,这是数控程序中常用的方法。
- 第一次走刀深
- 遵照样本中进刀表上的推荐值
- 更加“平衡‘’的切屑面积
- 后一次走刀实际约为0.07mm
2. 切深恒定
无论走刀次数的多少,每次走刀深度都相等。
- 对刀片有更高的要求
- 确保切屑控制
- 不应用于螺距大于TP1.5mm 或 16TP时
利用额外余量精修螺纹牙顶:
在加工螺纹之前,不必将胚料车削至精确的直径,利用额外余量/材料精修螺纹牙顶。对于精修牙顶刀片,前面的车削工序应留出0.03-0.07mm的材料,以使牙顶正确成形。

外螺纹进刀值推荐(ISO公制):
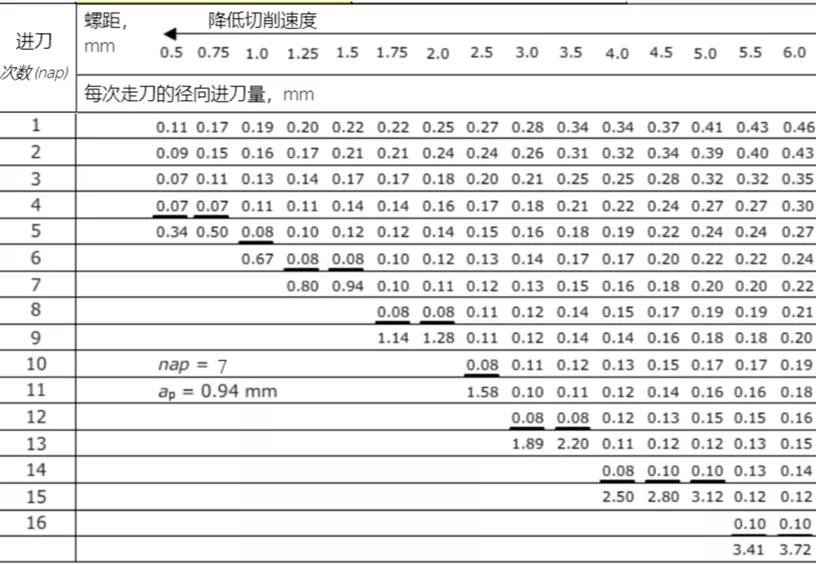
确保工件和刀具对中:
使用大中心线偏差±0.1mm。切削刃位置过高,后角将减小,切削刃将受到剐蹭(破裂);切削刃位置过低,螺纹牙型可能不正确。

五、螺纹车削应用技巧成功
1)在螺纹车削前检查工件直径是否有正确的加工余量,增加0.14mm作为牙顶余量。
2)在机床中精确定位刀具。
3)检查切削刃相对于中径的设置。
4)确保使用正确的刀片槽型(A、F或C )。
5)通过选择适当的刀垫确保足够大且均匀的间隙(刀片-倾斜刀垫),以获得正确的牙侧间隙。
6)如果螺纹不合格,则检查包括机床在内的整个装夹。
7)检查螺纹车削可用的数控程序。
8)优化进刀方法、走刀次数和尺寸。
9)确保正确的切削速度以满足应用要求。
10)如果工件螺纹的螺距错误,则检查机床螺距是否正确。
11)在切入工件之前,建议刀具应以3倍螺距的小距离开始。
12)高精度冷却液能够延长刀具寿命并改善切屑控制。
13)快换系统可确保简单快速的装夹。
为螺纹车削工序选择刀具时,应考虑:
- 检查悬伸和所需的任何间隙(例如台肩、副主轴等)
- 大限度地减少刀具悬伸以实现快速装夹
- 对于刚性差装夹,选择切削力更小的刀片
- 高精度冷却液能够延长刀具寿命并改善切削控制
- 使用即插即用冷却液接杆可轻松接通冷却液
- 为了提升生产率和刀具寿命,建议首选多牙型刀片,次要选择为单刃全牙型刀片,生产率低,刀具寿命短的选择是V牙型刀片。
刀片磨损和刀具寿命:
进刀方法,优化进刀方法、走刀次数和深度
刀片倾角,确保足够大且均匀的间隙(刀片-倾斜刀垫)
刀片槽型,确保使用正确的刀片槽型(A、F或C槽型)
刀片材质,根据材料和韧性要求选择正确的材质
切削参数,必要时,改变切削速度和走刀次数。
(原标题:【专业知识】金属车削加工螺纹的基本知识及要点!)