用机器人抓刀 通用技术集团沈阳机床复工挑战核心难题!
- 2020-03-16 09:50:406928
【机床商务网栏目 名企在线】3月6日,通用技术集团沈阳机床近40名一线安装员工和工程师组成的“沈北航空产业园重大项目小组”,正在沈阳航空产业集团园区内进行FMS0612u铝合金肋板类卧试加工中心的第6次机器人抓取刀具(简称抓刀)的稳定性测试。
FMS0612u铝合金肋板类卧试加工中心完全由沈阳机床自主研发,并全部实施系统国产化,技术成熟且自主可控,代表了国内机床领域进的制造技术。这次技术攻关将有效解决刀库故障问题,使换刀效率提高30%。
做第一个”吃螃蟹“的人
项目制造经理周兴福说:“这次我们测试的刀库与以往有很大不同,将改变机床换刀方式,为以后公司产品的升级奠定基础。”
去年年底,沈阳机床为沈阳地区“航空零部件加工重大项目”制造生产的22台机床全部交付用户现场。春节前,用于加工大型钛合金零部件的GMC2040ut龙门式五轴AB摆加工中心成功试切钛合金“S试件”,所有检测点全部合格。
复工后,小组成员对安装完成的第一条由6台卧式加工中心组成的铝合金肋板类加工生产线,进行了主轴头、转台和系统的调试,并在交付客户使用之前,再次对刀库进行测试。
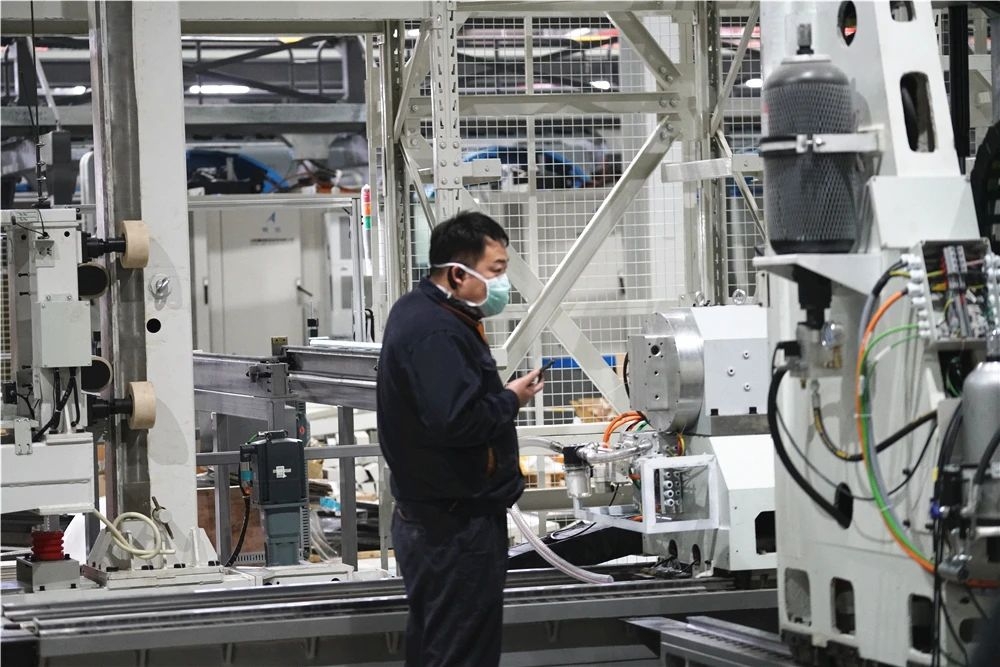
△技术工人正在客户现场调试机床液压系统
在国内机床行业,机械手臂一般都是上下料的过程中使用,几乎没有被用于换刀上。早在2019年12月份,沈阳机床便提出要把传统的链式结构刀库改一改。传统链式刀库采用液压驱动结构,故障率较高,虽然能满足客户的要求,但是沈阳机床的技术人员要突破这个难题,决定使用机器人替代传统链式刀库,使换刀更加稳定和精准。
周兴福决定做这个“吃螃蟹”的人,和其他党总支成员,包括电气设计室室主任马俊杰,机械设计主管刘丽英便在一起讨论该生产线刀库的调试方法。
反复测试,项目小组努力攻坚克难
12月20日晚上6点,项目组人员开始第一次对机器人换刀进行调试,第一个动作顺利完成,第二次抓取位置有些偏移,第三次不成功。原来,这面刀库墙有40个位置点,项目组以其中的三个点为基准让机器人确定刀具所在位置,可是这40个点的加工精准度达不到机械手要求的+-0.1mm,无法连贯的完成换刀动作,虽然经过一晚上的调试,换刀的动作有改善,但并没有达到项目组预期的要求。
“必须重新做基准。”周兴福说,随后,项目组尝试在刀库墙上加装新的调试校正基准,他们试过球形、长方形、正方形等许多方案。

△周兴福正进行机械手在刀库墙侧抓取刀具动作的测试
2月21日,经过5次技术上的改进,项目组确定使用三点式可调节基准面作为校正机械手坐标系的基准,便于后期设备维护和基准校正。
3月初,项目组按照设计方案做出了全新的刀库墙并进行第6次机器人抓刀的稳定性测试。测试结果非常理想,无论是刀具的路径,刀柄的抓取动作,还是刀库和机床的节拍一致性都通过了测试,使机床的换刀效率提高30%,稳定性提高30%。

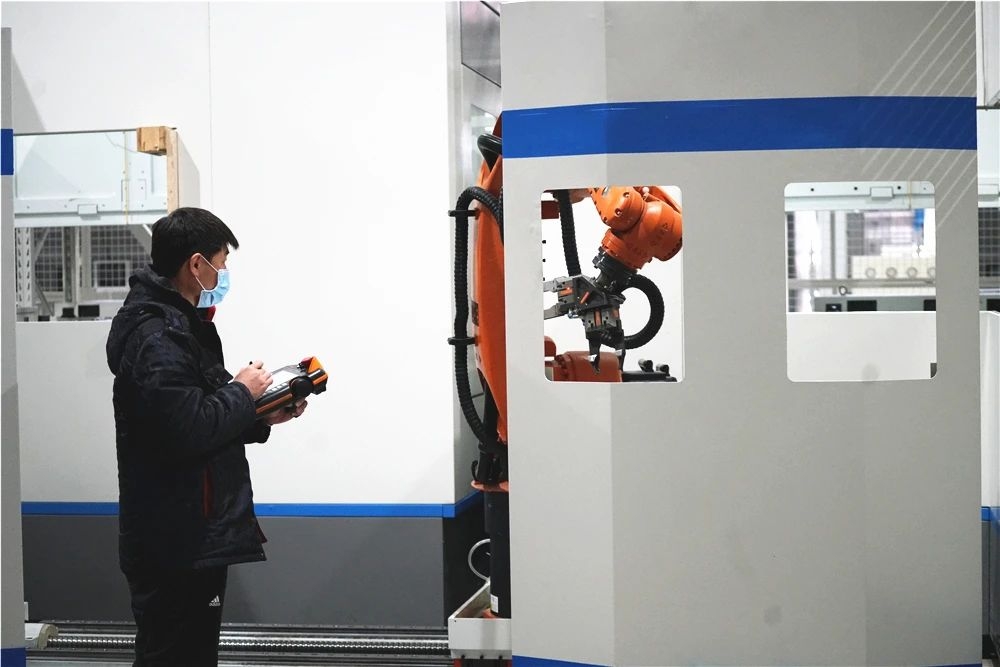
△沈北航空产业园重大项目小组党员正在对机器人抓取刀具进行调试
目前,第一条由6台FMS0612u铝合金肋板类卧试加工中心组成的铝合金肋板类加工生产线已经交付客户验收,还有两条生产线正在安装中。正是项目成员进行一次次的尝试与挑战、创新与突破保证了项目的进展,才使国产设备逐步替代进口成为可能。
(原标题:用机器人抓刀 通用技术集团沈阳机床复工挑战核心难题)