冷却液如何改善螺纹车削性能
- 2019-12-20 16:14:2011785
【机床商务网栏目 科技动态】螺纹加工在各行各业都普遍存在。尽管螺纹车削已经有几十年的历史,但加工过程仍在不断进步,以满足难加工材料(如不锈钢、高温合金和钛合金等)的加工需求。螺纹车削刀具的上供冷却液和下供冷却液组合,会延长刀具寿命,提高螺纹质量,并且有提高切削参数的潜力。在加工难加工材料时,这种积极效果更加明显。
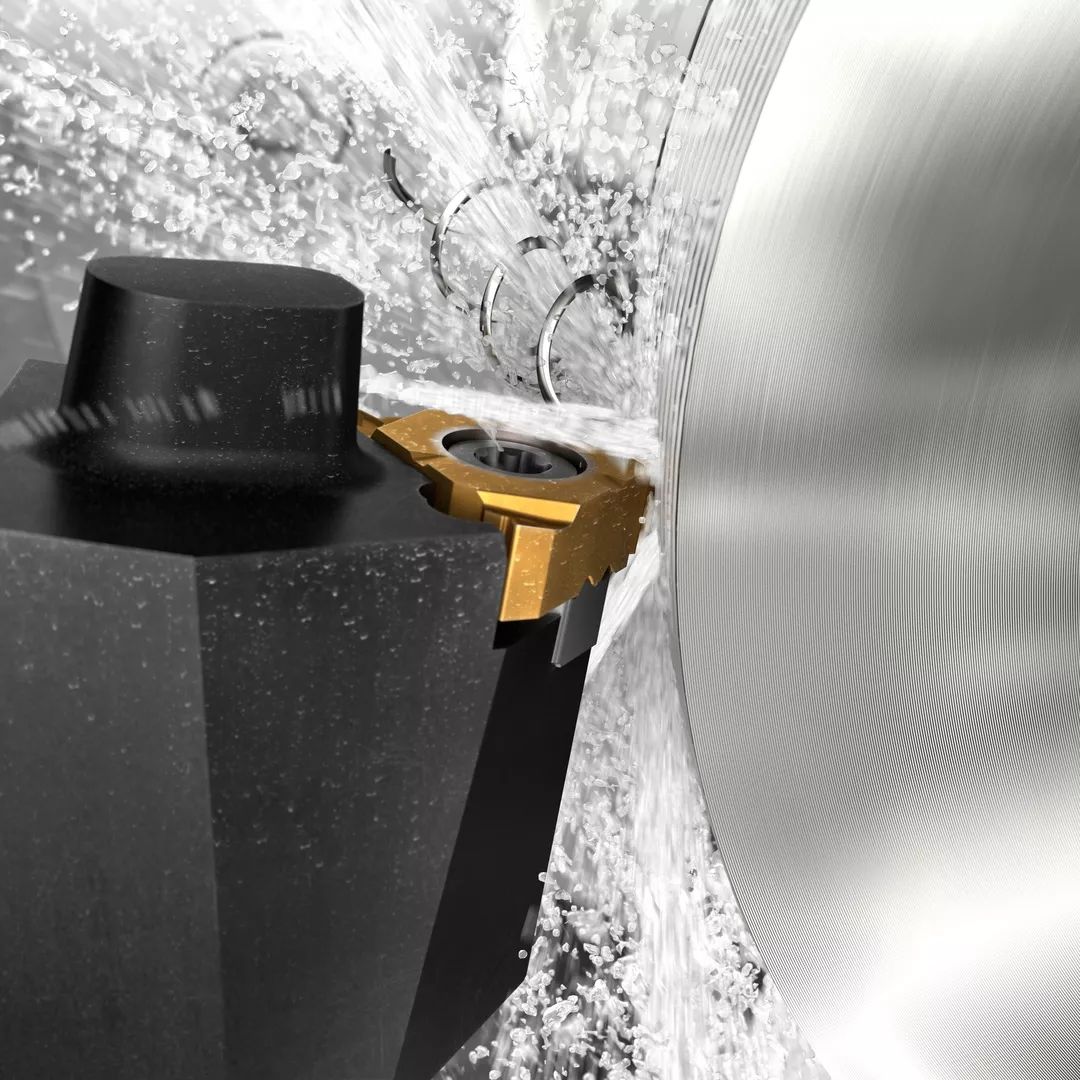
不锈钢材料(ISO M)、HRSA材料和钛合金材料(ISO S)存在很多加工性问题。就 ISO M 材料而言,加工性往往随着合金含量的升高而降低。铁素体/马氏体材料的切屑控制不难,但是在奥氏体和双相不锈钢中,切屑控制就很复杂。麻烦的是,加工这些材料会产生较大切削力,同时还会出现积屑瘤和加工硬化表面。这些因素都会影响刀具寿命。
关于ISO S系列材料,由于合金的化学性质和材料结构,每种材料的物理性质和加工特性大不相同。例如,退火和时效对加工特性有很大影响。众所周知,加工ISO S材料切屑控制具有挑战性,所需要的切削力和功率也很高。

保持高压冷却
很显然,在加工ISO M和ISO S材料时,使用冷却液是非常必要的。而且,山特维克可乐满的专家能够证明,采用冷却液对螺纹切削工序会带来大量额外好处。此时的重点是精确度,利用不同方向的冷却液(靠近切削刃),满足不同的具体要求。
在使用新引进的CoroThread® 266系列刀具进行外螺纹车削时,该技术的优势十分明显,高精度上供冷却液和下供冷却液,可改善加工过程安全性,提高效率。上供冷却液可改善成屑效果,清除切削区域的切屑,确保加工更加安全,无故障,减少非计划停机;下供冷却液可控制温度,确保刀具使用寿命长且可预测。这种高精度冷却液的配置对表面光洁度也有积极影响,可生成高质量螺纹,这种创新技术的附加好处是刀具的切削参数更高,从而缩短了加工时间。
加工过程的稳定性
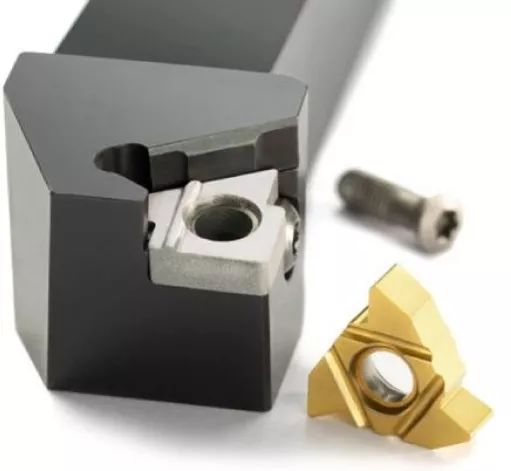
除了高精度冷却液外,稳定的加工过程对螺纹车削一次成型也很重要。因此,CoroThread 266 在刀柄与刀片之间采用的iLock®接口,此结构可防止刀片座内的刀片微小运动,从而提高精度、表面光洁度和一致性。

有证据表明,高精度冷却还能解决螺纹车削的其他问题。例如,那些一直在设法解决切屑控制和表面质量问题的客户,一定能从上供冷却液的应用中获益,因为这种冷却方式有助于排屑,可避免因切削引起的缺陷。那些遇到尺寸问题的客户,通常是因为刀片温度过高,导致刀片磨损过快,他们会从下供冷却液的冷却效果中受益。上供冷却液和下供冷却液的盈利潜力都很大。
在测量ISO M零件螺纹车削时每件零件的后刀面磨损的试验期间,我们将标准外供冷却液与高精度上供冷却液和下供冷却液之间的结果进行了比较。冷却液压力为40 bar(580 psi)时,与使用外供冷却液车削螺纹相比,采用高精度上供冷却液车削螺纹,后刀面磨损明显少很多。使用高精度下供冷却液时,后刀面磨损还要少。平均来看,刀片寿命几乎翻番。
测试表明,使用高精度冷却液在刀片寿命方面,得到很大的改善。这种效果在大量客户试用过程中得到证实。
客户试用结果
有一家客户,在SS2333材质不锈钢零件上车削Whitworth管螺纹(G 1¼英寸),与好的竞品相比,刀片寿命获得很大提高。另外,即使压力在10 bar(145 psi)以下,使用CoroThread 266,也能大大改善切屑控制,即使采用与以前相同的方式车削,切屑也不再粘在零件和/或刀具上。切屑粘在零件和/或刀具上时,会导致零件的表面损伤,或者导致切削刃与零件之间堵塞,从而引起刀片断裂。
另外一家客户,在AISI 422不锈钢工件上车削UN 螺纹(60°,3½英寸,8 TPI)时,刀具使用寿命延长很多,切削速度明显提升。在采用高压冷却液运行时,客户反馈非常满意所达到的效果,而且切屑控制也好很多。
其它客户使用表明,在316L不锈钢零件和Ti6Al4V钛合金上进行螺纹车削时,刀具寿命也会延长很多。
其它材料

除了难加工的ISO M材料和ISO S材料外,钢(ISO P)件同样推荐使用高精度冷却技术,其效果也被另一家客户得到证实。尽管压力较低,仅有7~10 bar(102-145 psi),在AISI 1215非合金钢上车削1英寸的NPT螺纹(11½ TPI)时,见证了刀具使用寿命大大延长。
在使用ISO P材料进行试验时,将压力为40 bar(580 psi)的高精度上供冷却液和下供冷却液与标准的外冷应用相比,后刀面磨损大幅降低。试验表明,冷却液压力在10 bar以下也有各种好处,但是70 bar的高压冷却在降低平均后刀面磨损方面更加优异。
归根结底,高精度冷却液可有效降低切削刃产生的热量,并可增加切削速度,从而提高生产效率,并保持刀具使用寿命。此外,高精度冷却液还有助于清除零件和刀具的切屑,改善切屑形成,从而增加了加工过程的安全性。
(原标题:冷却液如何改善螺纹车削性能)