工匠的手工加工精度真的比数控机床厉害吗?
- 2017-06-13 13:53:0818561
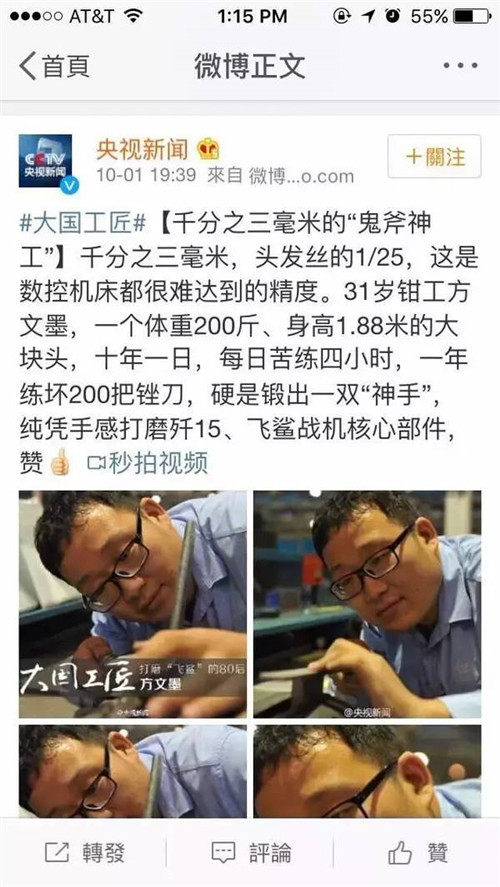
有的网友说:“造假!和那些采访太极拳大师的视频一样一样的!”,也有的网友认为,只有在制造机械落后的国家才会如此的依赖人工,宣传颂扬这些厉害的匠人不利于鼓励科技创新......看到这些评论之后,相信不止涉世未深的小编也是疑惑重重,很多网友也是一头雾水。基于此,小编遂请来活跃于网络的诸位业内人士各抒己见,达到在不断交流中接近真相的目的。下面,就请大家先看看他们都说了些啥?
网友LovelyHibiki:
我认为一些入行多年的能工巧匠确实能够做出比较精细的工件,但是,手工是永远无法达到机械加工的精度和稳定性的。闲话少叙,看下面的例子,用事实说话!
下图是长春光机所生产的高精度中阶梯光栅,每毫米有6000道均匀的刻槽, 刻槽间距误差小于一根头发丝的千分之一,加工时仅仅是工匠手的温度带来的误差就足以破坏光栅的一致性了。
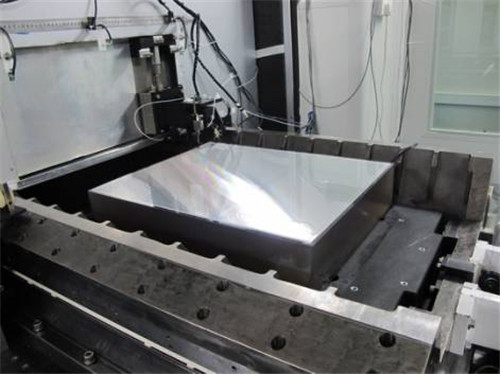
完成它的是长春光机所承担的国家重大科研装备研制项目“大型高精度衍射光栅刻划系统”。
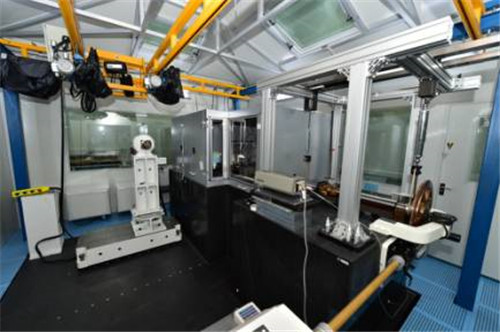
大型望远镜和空间光学系统的反射镜片,一般用铝、铍或者碳化硅制成镜坯,然后用高精度磨床将其磨成所需的形状。
下图是长春光机所研制的4m直径碳化硅镜坯。
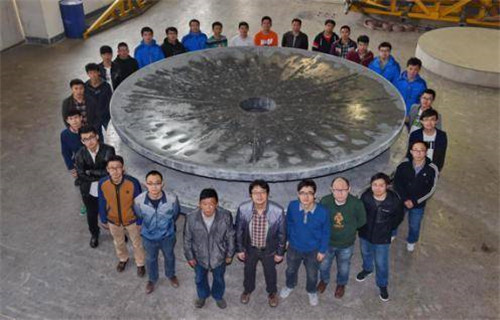
下图是人类空间光学的造物,预定于明年十月发射的詹姆斯韦伯太空望远镜的6.5m铍反射镜,放在这里作为镜片加工完成的例子。
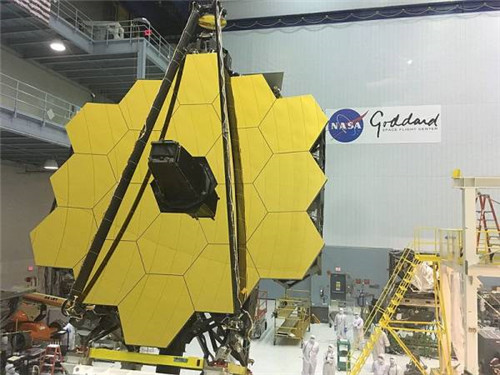
不管是吉林一号、高景一号、地球之眼这样普通的遥感卫星,还是NRO的锁眼侦察卫星,亦或是披着遥感X号或高分X号马甲的某些卫星,当然也包括上面这块将要运行于拉格朗日点的太空望远镜,他们不分中外不分高低贵贱,镜片加工精度都至少要达到他们所使用光波长的十分之一这个量级,也就是约20nm,有的还要更高,比如NRO的丢仓库的垃圾镜片都能让NASA捡去当宝。而这20nm的误差,仅有工匠眼球上的50个水分子宽,比工人手指毛细血管搏动时的尺寸变化还要小得多,而且工件需要加工成的形状不是平面而是抛物面或者为某些用途精心设计的复杂曲面,你让个人来加工试试看?
后放个上帝也无法手工加工出的零件:
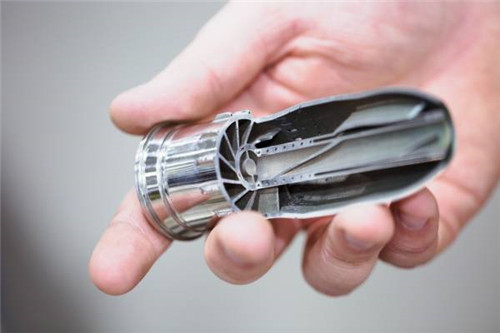
GE高精度3D打印一体式燃油喷嘴,注意这是展示品,真货是内部形状相同的封闭结构。
网友JackyQ:
这个说法,也对也不对。
从对的角度来说,其实所谓“匠人”的日本工业领域的角色就是如此,不仅在机械打磨、装配方面,甚至还在电子领域,日本的部分军用的芯片电路是人在显微镜下制造出来的。在开发领域过去也有很多这样的匠人,比如说科研和测试开发用的很多电子电路由于只需要几片十几片,无法采用非常先进的设备制造,而普通制造方式故障率又高,所有有不少拿着手提箱的老专家,科研单位打电话请来之后在放大镜下面默默地焊接电子电路,我看过这个质量真心赞。这个工作在十几年前各大科研机构攻关自主开发柴油机/汽油机电控系统时候蛮多的,现在比较少了。我在技术评审一些很老的企业的时候,很多零部件需要考虑动平衡,然后就有完全参考动平衡机的动量偏置后纯靠手感打孔平衡的老师傅。
但是反过来说,千分之三毫米,其实也就是3u,在汽车领域虽然算高,但也不算是什么特别高的精度。高速旋转的摩擦副表面如果采用了超精磨+抛光带的话,圆度一般在4-8u左右。而下图是目前我生产控制中高的形位公差要求:
谁来手工挫一个我看看?(而且是PQC值哦,一年你要挫一百多万个哦!)
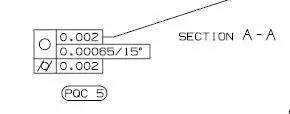
接下来我们说这个图片:
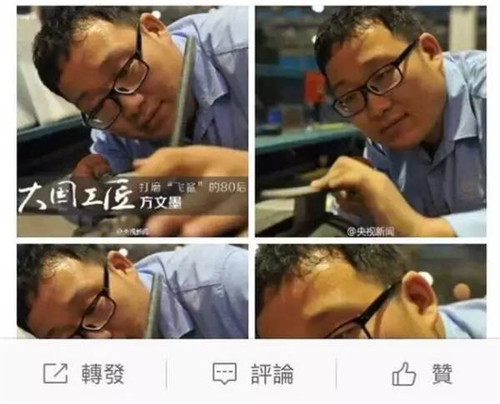
我觉得这个照片应该是摆拍的。
为什么3u的精度很难。在实际制造中,根据我的经验,4-8u的制造精度主要是设备的稳定性,而4u以下的制造还必须加上温度补偿。3u不仅制造困难,测量也困难。所有我的供应商,走进测量室没有温湿度机的我扭头就走,评审会议就是当着总经理的面说你们测量室根本不值一看。4u-8u要求有效温控测量,一般为20+/-2度,4u以下要求恒温室测量,要求20+/-1度。对于4-8u加工主要看设备,而4u以下的尺寸和形位公差要求,必须具备加工时非接触式的温度测量以及自动式的加工余量补偿。那么从制造困难角度来说,除了稳定性外,还有很大一部分的难度是定位和其他的加工补偿。
但是如图中,使用的是简易的台虎钳,锉刀也是粗糙的锉刀,师傅的额头还有谜之反光(是热的么?),按照如图挫出来的零部件,应该是不可能纯靠手工加工达到所谓3u的精度的。无论师傅的手感多好,台虎钳所装夹的装夹面很差,波动抖动都很厉害,而且现场根本就没有温控手段,表面质量也会很差,这种战斗机你造出来就是害人。
所以我大胆的假设一下,这个所谓的3u是否是机械加工到一定程度,然后师傅用锉刀和精抛带做一些后续加工修正。比如说加工到30+0.01,然后手工顺着这个平整面一点点往下抛,抛到30+0.003以下。其他的形位尺寸要求可能会宽一点之类的,然后通过测量手段来筛选合格品。所以所谓手工能达到这个精度,我觉得本身也有一些宣传的噱头在里面。
我在国内走的机械制造类的工厂,从兵工相关国企、跨国企业、各地首富投的私企也不下五六十家了,目前还没看到那家和我说他们的技师能够手工加工到这个精度的。而是不停的在我的建议下采购几千万到上亿投资额的生产线和样品线。
其实大众们也应该要了解,兵工行业和常规的制造行业还是有区别的,飞豹造的再多也不可能一年七八百万的规模来制造,一年就小几百,购买我说的那种机床国家没有这个信心和投资能力,因为这可能只是一个非常小的零部件而已。能手工的就手工了,而且可以造几百个根据尺寸测量结果后筛选出一个就好了。
不用考虑我们普通制造业所关心的内费、外费等等,所以就好比我一开始说的那样,可能你是被迫必须要选择手工制造,而不是说因为手工制造好所以不用数控机床。
后就是抛弃用途谈精度是错误的,如果你确实用不到这个精度,那么也就没有必要上这么高的手段了。
自动化制造是大方向,这个谁也改变不了。我觉得可以考虑的是将军工制造的民间参与度进一步提升,国家资助国内的制造业企业提升制造,在民用提升的同时借用提升军用制造能力。起到一分钱当2分甚至1毛钱花的效果。
以上就是我的一点粗浅的看法。
匿名网友:
精加工领域的忍不住了,来说两句。
有一个逻辑性的问题,讨论起来比较有意思。“工匠比数控机床还”这里的指的是终的加工结果,而工匠加工和数控机床加工是对加工方式的描述。那么这里的逻辑很简单了,加工方式直接决定加工结果吗?并不全是,因为诸位都漏下了加工中重要的一环,即补偿加工(也就等价于控制系统中的反馈环节)。
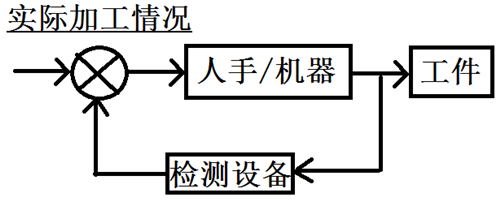
那么我们就回到了初的问题,终的加工的精度由什么决定?人手还是机器来做这件事都是执行的环节,决定加工精度的还有检测反馈的环节啊!于是就有以下的情况:
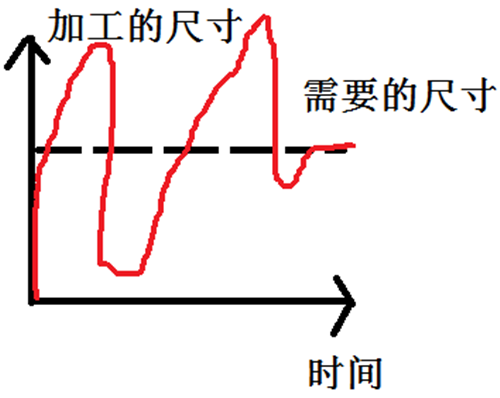
像上图一样,执行器的精度低,每次误差多大看心情,但测量设备的精度高,每次误差多大都能准确测出。这种情况就比较像人手来操作了,每一次加工的误差都可能会很大,奈何设备牛逼,每一次加工的误差有多大都会修回来,如果是熟练的技工大叔的话,在牺牲了一定时间以后,精度肯定是可以保证的。
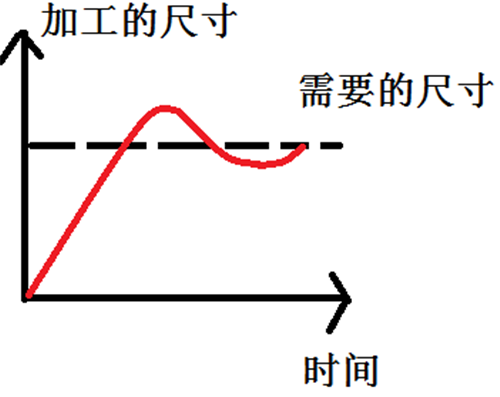
上图这种情况就比较像机器了,执行器的精度高,测量设备的精度也高,每次加工后会有误差但误差都非常小而且稳定,一般情况下比人手加工要强。
那么人加工就不如机器加工了吗?分场合。
有一个例子,在加工工件时为了把工件的回转中心和主轴的中心放在一条直线上,一般我们会拿小锤去敲工件,再拿千分表去测,反复几次就能把误差调到3um以下。有一个法国研究生应该是只在工厂中实习过,来时候就很傲慢地说我们国家都用的专用夹具来生产产品,你们这个精度太低了。须知道这样的结论是非常可笑的,一般工厂的精度只是10um的量级(也就是丝),夹具本身装夹也有误差, 终的装夹结果没有手调的精度高。因为我们会根据千分表的反馈去调节,而夹具设计地再好精度也有限。
机器加工有自己的局限。例如用一个机床来加工导轨,该机床的导轨1000mm长直线度10um左右,那不做任何外部调整,用这个机床加工出的1000mm长导轨直线度不会优于10um,因为机床本身的误差会被复印上去。这种情况下方便的方法就是让熟练的技工大叔用手去磨。当然,设计一个伺服机构来在位补偿加工也是一个解决方案,但是当精度达到纳米量级,首先这种设备就不好制造,能不能造出来都两说;其次成本啊!技工大叔说我一天三两二锅头四斤猪头肉一人吃饱全家不饿,造这么牛逼的设备够养活好几十个我了!
这样的例子有很多很多,哪个更还要分场合。工程的问题很多都讲求一个trade-off,没有好,只有更适合。外行人看机械这门学科容易产生的误区就是脱离实际情况,直接下结论哪个更强,须知这种结论是很武断的,尺有所短寸有所长,合适的才是好的。
小编:
感谢以上三位“大神”的专业分析!相信大家在看了以上不同角度的分析之后都对这个问题有了更深的理解,也一定有着很多个人的观点和看法。在机械行业中,由于加工的环境、技术、器材和要求等等的不同,所有的问题都不是表面上那么简单,可以一句话就回答清楚。所以,多多讨论才有利于大家共同进步。
后,对于这个问题您心目中自己的观点和看法是什么呢?欢迎在文章下面留言讨论。
(资料来源:知乎问答 LovelyHibiki JackyQ)